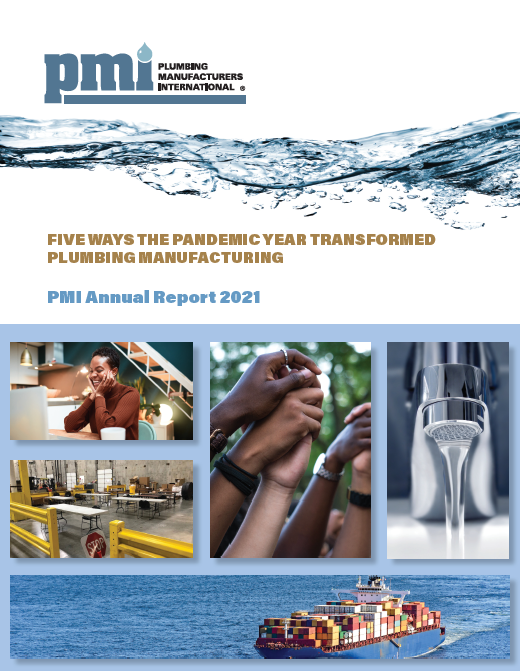
During a turbulent time, we rallied together to prove PMI is for you
The pandemic year was as turbulent a time as the world has seen. By taking care of each other while tending to our business, we helped to slow the spread of COVID-19 while contributing to economic healing.
This 2021 PMI Annual Report explores the ways the pandemic year transformed the plumbing manufacturing industry and how PMI members adapted to these changes with PMI’s help.
At the beginning of the pandemic, PMI played a central role in keeping manufacturing facilities open and available, using its many professional relationships and alliances to gain access to federal and state decision-makers.
PMI pointed its members to reliable information about how to operate manufacturing facilities safely in the midst of the pandemic. Already operating virtually, PMI staff continued business as usual as members transitioned to remote working, again sharing insights through webinars, committee meetings, and publications.
As PMI members innovated to address concerns about infection spread, PMI continued to advocate for tariff relief so that members could gain access to needed materials. Not only did PMI members keep their employees safe and businesses running smoothly, many stepped up and quickly shifted gears to produce much-needed personal protective equipment (PPE) for front-line workers.
And as citizens across the globe gained an awareness of the need for better social justice, PMI and its members instituted programs to improve diversity and inclusion (D[&]I) throughout the industry. Not only are strong D[&]I efforts the right thing to do, they produce better results for our members and industry.
None of these accomplishments and initiatives would be possible without your company’s support and the involvement of your employees who volunteer to take on leadership positions.
Within the past year, Brasscraft Manufacturing Co., Dornbracht Americas, Inc., Elkay, and UL became PMI’s newest members. Bob Neff of Delta Faucet Co. joined our board of directors, Ned Dickey of Hansgrohe, Inc., became a co-chair of the PMI Technical Committee, and Anish Desai of IAPMO became a co-chair of the PMI Allied Member Committee. Stephanie Lass joined the PMI staff as education coordinator, bringing a strong addition to the contributions Kerry Stackpole, Matt Sigler, Jodi Stuhrberg and Ann Geier deliver every day.
These companies and individuals joined a core team that has served PMI so well over the years. This report features some new faces with whom we hope you’ll become acquainted.
During normal operations and throughout turbulent times, PMI is for you – and every employee of your company. We hope this report provides insights into PMI’s important role in our industry and why your continued support and involvement is so vital.
Todd Teter
PMI President
House of Rohl
[nbsp]
Joel Smith
PMI Immediate Past President
Kohler Co.
[nbsp]
“How do we make sure our industry is available?”
Looking back to the beginning of the pandemic year, PMI CEO/Executive Director Kerry Stackpole remembers asking that question. “When you’re in a pandemic, and you’re relying on hand washing and hot water to keep it at bay, plumbing products fulfill an urgent need,” he said.
“My days were spent reaching out to my contacts in government and peers in the plumbing industry association community,” he recalled. “We talked about the best ways to assure that plumbing manufacturers were known and designated as essential businesses.”
Soon, Stackpole was in direct touch with Chris Krebs, the head of the Cybersecurity and Infrastructure Security Agency (CISA) at the Department of Homeland Security. In an exchange of emails, Stackpole alerted him about the essential role plumbing manufacturers could play in the pandemic and reminded him that plumbers had already been identified as essential workers. “And he got it,” Stackpole remembered. “The good news is, he got it right away.”
With plumbing manufacturers added to CISA’s “Essential Critical Infrastructure Workforce” advisory list, the next challenge for PMI and its members was gaining the support of governors in about 10 states where PMI manufacturing facilities were located to follow the advisory and stay open. In a similar effort, PMI worked with the National Association of Manufacturers and U.S. government trade officials to urge Mexico to recognize manufacturers as essential businesses and keep PMI member facilities open. Stephanie Salmon, PMI federal government affairs consultant, spearheaded this work.
Amid much speculation and conflicting information during the first few weeks of the pandemic, PMI kept members informed through its usual communication channels – committee calls, website, publications, alerts and social media posts – as progress was made on behalf of the industry and as guidance, resources and other critical information were made available.
PMI surveyed members about expected impacts of COVID-19 on production, travel and other measures, and fed back the aggregated, de-identified information back to them “so they could understand what was going on in our industry,” Stackpole said. “We put whatever education we could find in front of our members, to help them cope with what was going on with COVID-19. All of those things combined allowed us to keep moving. That was encouraging, from my standpoint, in the sense that members could still reach out. They could still talk to each other. We were becoming a conduit for the members who had been sent home and were working alone. Their ability to gather with us on our calls and work with our teams, I think was a valuable connection for many of us.”
Providing connection and comfort during an outbreak
PMI shared important information to members about their having been designated essential businesses. “As a supplier, we were considered an essential business, which led us to keeping our Atlanta operation running. It was good to hear that everyone in our industry was thinking the same way – keeping our doors open and making our products accessible to meet market demand and plumbers’ needs,” said Maja Jankov, product manager, Duravit USA, Inc.
When the COVID-19 situation broke, PMI was Haws Corp.’s first stop, said James Burwell, senior global product manager. “We wanted to be recognized as an essential business, so Kerry drafted a letter explaining our essential status,” he stated.
Belinda Wise, director of business development North America, Kerox, Ltd., said her company is grateful for how supportive and informative PMI has been during the pandemic. “It’s wonderful to see PMI playing the role of a central communications point on COVID-19 updates and how our industry is being affected. It’s comforting to know that companies can reach out to PMI for help and support.”
1. Plumbing manufacturers transformed workplace safety precautions to meet the COVID-19 challenge
With the essential business designation from CISA secured, the responsibility for conducting manufacturing operations in a safe manner fell on PMI members. Following guidelines issued by federal, state and local authorities, PMI member companies implemented precautions designed to reduce the spread of COVID-19. They secured and issued face masks and other kinds of PPE to employees, reconfigured workspaces and erected barriers to achieve physical distancing, started taking temperature checks, stepped up disinfection and hand hygiene, improved airflow and ventilation, and staggered shifts to reduce the number of workers inside facilities.
At LIXIL facilities across the globe, a “safety first” message was driven by the company’s leadership team. “I specifically have a memory of sitting in my office the day we had our first (COVID-19) case,” noted Chris Marozzi, leader of employees’ health and safety for LIXIL Americas. “This was a total team effort – our communications team, our legal team, our HR team, our plant vice presidents – all of these groups were fully aligned to protect our people first.”
The LIXIL team realizes that keeping its people safe best protects the company’s ability to produce. The company assertively implemented a policy to quarantine any employee exposed to potential COVID-19 infection from the workplace for 14 days, with full pay. Because of the shortage of COVID-19 testing, LIXIL chooses not to wait for a positive test, instead quarantining individuals who exhibit symptoms or who are found via contact tracking to be near others who test positive. “It was tough because we had to send home (many) people, but the long-term thinking was that it kept the rest of our people safe and kept our plants operating,” Marozzi stated.
As a global company, LIXIL shares best practices from around the world with each of its facilities, including data from Japan and other nations where populations are used to wearing face masks. LIXIL tracks the number of quarantines and COVID-19 cases in each plant, as well as cases in the counties and states where plants are located, Marozzi said. These data enable LIXIL to dial production up or down to match the number of workers who are available.
To encourage compliance with COVID-19 precautions away from their facilities, LIXIL provided education about COVID-19, as well as masks to employees for use by themselves and their families. Using its 3D-printing capabilities, LIXIL also manufactured 72,000 face shields and donated them to first responders, healthcare workers, educators and others for additional protection. For employees of their manufacturing facilities, LIXIL provided sanitation kits for use at home and educated them about the risks of traveling, especially during the holidays.
LIXIL has begun to educate its employees about COVID-19 vaccines, as the rollout continues throughout the world. In the meantime, Marozzi said the company will continue to be cautious, considering the unknown effects of COVID-19 variants and other factors. “I think it’s going to be another year, at least, of maintaining masks.” He added that hygiene stations, plexiglass barriers, improvements to airflow, and other measures may be here to stay in case of future epidemics, especially since data show that these measures significantly reduced flu rates while slowing the spread of COVID-19. “I will strongly advocate for keeping the things that are logical in place,” he stated.
The company provided two global payouts to all employees, one in April 2020 and another in February 2021, said Debbie Drury, leader, communications and corporate responsibility, LIXIL. Each employee received the same amount, in recognition of the challenges of navigating life and work. “It’s consistent with what the company has been saying all along; the safety and well-being of our employees is the number one priority,” she stated.
2. The remote working experiment was successful – and is here to stay for many
Like many other PMI members, Kohler Co. has operations and offices around the world. This global presence placed Kohler employees in the path of previous regional epidemics, such as SARS in 2002-2004 and MERS in 2012. These experiences resulted in the company developing an infectious disease pandemic policy which, along with having staff in China when the COVID-19 pandemic started, guided the company’s global response.
Kohler put protocols and measures into place to ensure safe operations during the pandemic but allowing for regional adaptation, said Brian Kendall, Kohler’s director of operational excellence. As the pandemic spread worldwide and became increasingly lethal, “we needed to quickly adapt to a different operating environment, and we successfully did that,” he stated.
Adam Guenther, Kohler’s associate director, operational excellence, said the company’s incident management team was monitoring COVID-19 case counts around the world. These data drove Kohler’s decision, during the second week of March 2020, to transition all administrative associates in the United States who were able to work remotely. “We had a process in place for people to take the company’s assets off campus and use them in their homes. We already had been working in the Microsoft Teams environment, and we were able to successfully use Teams as a tool to support the new model,” Guenther explained.
Both Kendall and Guenther emphasized the positive consequences of shifting into remote work. “We saw an increase in the use of collaboration technology,” Kendall said. “Interactions grew significantly as we got better at it. Our decision-making improved, with colleagues being able to make decisions in real time, driving productivity gains and results.” Guenther said the company was surprised at “the intensity of work people were able to do from home. There was little to no loss in productivity because people were able to generate an increased number of work hours compared to where they were before,” to the point where the company encouraged employees to place boundaries on their work lives, he stated.
Kendall expects post-pandemic work life to be a hybrid between pre- and post-COVID. “That’s something we are taking a hard look at. I think that there are very few companies that are not going to be responding with a hybrid version. (Kohler associates) don’t miss their commute time,” he said, “but I know many associates are ready to get back into the office to be with colleagues – they do miss that face-to-face interaction.”
During a panel presentation at the PMI20 Manufacturing Success Conference, remote work expert Laurel Farrer said the pandemic resulted in about 86% of American employees working from home during the pandemic, with 40% to 50% of them expecting to continue this work arrangement post-COVID-19. “Those are incredible numbers that affect millions of people,” she stated. “We don’t have regulations or legislation to protect either the employers or the employees at this scale. So there’s a lot of catching up to do” in both the private and public sector.
“The office as an institution is not going anywhere anytime soon. It’s not a matter of if we have offices in the future, it’s a matter of how we are using them,” Farrer said. Farrer and the other panelists presenting at PMI20 agreed that offices will likely be reserved for collaborative tasks – group decision-making, strategic thinking, product innovation, and research and development. “But we have now moved out of the historical era in which we need to drive an hour and a half to sit down at a computer to input data into a spreadsheet. That’s what’s going to change,” Farrer stated.
3. Concerns about infectious pathogens drive product innovation
While causing challenges on production lines and forcing a shift to remote work, the COVID-19 pandemic created opportunities for the plumbing manufacturing industry to address a newfound concern many people now have: the spread of infectious viruses.
Once out of sight and out of mind, invisible sources of infection are now top of mind among many people. A survey conducted by PMI member Bradley Corp. found that most Americans have responded to virus outbreaks by washing their hands more frequently, more thoroughly and longer. More hand washing leads to more scrutiny placed on bathrooms, especially those in public places.
“A customer may say, ‘Hey, you know, I don’t want to use your restroom because I have to touch it,’” said Nate Kogler, senior director of product management at Bradley. This mindset is more than someone reacting against an unclean sink or restroom. It’s more about people being “more aware of what they’re touching at all times,” he explained.
This change in public awareness has caused a spike in the sales of touchless plumbing products, with many PMI member companies reporting increased sales of both faucets and toilets with touchless features. “Touch-free is everywhere. It’s in every conversation. That’s foremost in driving many of the innovation efforts at Bradley and throughout the industry,” Kogler stated.[nbsp]
Mark Lawinger, Sloan Valve Co.’s senior product line manager for flushometers and fixtures, said COVID-19 is “dramatically changing how everyone looks at public spaces, and there will be an even stronger call for clean and hygienic restrooms.” For example, “we’re seeing locations that have manual flushometers now utilizing Sloan’s retrofit flushometer kits to transform their restrooms into touchless spaces because users are not willing to touch the flushometer handle,” he added.
During the PMI20 Manufacturing Success Conference, Steven Soifer, Ph.D., president of the American Restroom Association (ARA), gave his thoughts about how restroom design is likely to change. He highlighted the ARA’s proposal that suggests the United States incorporate the European design of single-occupancy toilet rooms. Soifer said the typical European public restroom, with six individual stalls and two ADA-compliant stalls, costs the same as the traditional gender-segregated restrooms in the U.S., but uses 25% less space.
Still, with many multi-occupancy bathrooms still in service, users of these facilities are faced with toilets, urinals, sinks and air dryers dispersed throughout the room, with no clear flow as to how visitors use them. “You have a lot of people crossing into each other after using a toilet or urinal, and then washing their hands in one spot and drying them in another,” Kogler explained. One Bradley product innovation addressed this situation, with a faucet, soap dispenser and focused, hi-speed hand dryer built into a simple bar placed at the top of a sink. This solution eliminates soap and water falling onto the counter and the need to walk away from the sink to dry hands. A winner of a 2020 Good Design Award, this application can be built adjacent to a toilet to reduce foot-traffic flow within a public facility even more.
In addition, PMI members increasingly use materials that resist bacteria growth and have developed self-cleaning toilets, sinks designed to drain water quickly, and counters without narrow gaps that are difficult to clean or disinfect.
As individuals put money into their bathrooms instead of vacations or live entertainment during the pandemic, new plumbing products have gained momentum on the commercial side, too. “It’s tied very closely to customer satisfaction with the business,” Kogler stated. “Owners understand that their customers remember what the washroom looks like. They’re going to say, ‘this store has the cleanest bathrooms. I enjoy shopping there.’”
4. Shutdowns, tariffs cause companies to rethink supply chains
With PMI member companies already dealing with supply chain disruptions caused by tariffs on Chinese goods, the COVID-19 pandemic created “havoc in every possible way,” said Elton Perkins, director, global sourcing and distribution, Fluidmaster, Inc., and co-chair of PMI’s Commerce Committee.
The tariffs created pressures to either negotiate with a customer or figure out how to absorb the cost. “As a company, you have to decide how you’re going to deal with margin degradation. But it didn’t force us to change the supply chain,” Perkins stated.
COVID-19 has been more disruptive than the tariffs because of the shutdowns. “Mexico implemented red, orange and yellow grades of shutdowns and other countries like Turkey completely shut regions down because of growing cases,” Perkins said.
The shutdowns reduced the availability of raw materials – which in turn reduced the availability of shipping containers, which were retained by customers to store inventory they couldn’t sell. “You start removing containers from the supply chain and you fast forward six months, nine months, and there’s no containers in China to export. Couple that with Chinese New Year, and you’ve got a massive global problem on the ocean freight level,” he explained.
Rapid and unexpected developments caused by the pandemic have forced companies to monitor their supply chains continuously. “I have to look at all the raw materials that we need to make a product,” Perkins stated. “How many sources do I have for ABS (acrylonitrile butadiene styrene) or polypropylene, for example? Do I have enough qualified sources in my spec, so that if one supplier shuts down, I can choose a second? Frankly, I’m having to go three to four deep on various raw materials and qualifying a backup, and backup to backups, of suppliers to critical raw materials. And it’s constant.”
This situation causes a dynamic similar to a traffic jam, where a disruption in one place creates reverberations that echo through a much greater area. Perkins said a leading producer of ABS decided to downsize and shut down production lines at the beginning of the pandemic to avoid an over-inventory of material. “Fast forward six months, and you’ve got markets reopening and demand going up. The (producer) can’t fire up fast enough and then blew through the inventory. Now, everyone quickly has to find another supplier,” he explained.
Similar dynamics are in play on other kinds of material, causing trickle-down effects all the way through distribution. “People are buying everything that they can possibly get their hands on” while the demand is available, causing spikes in prices, Perkins said.
Despite the challenges of running supply chains through China, Perkins said the price of certain kinds of raw material, such as silicone, makes sourcing it within the United States or even Canada or Mexico prohibitive, even when factoring in the cost of tariffs. U.S. steel, copper and brass face stiff competition globally. “But production of plastic resins and injection molding, because it’s mainly machine operated, absolutely can come back to the United States,” he stated.
Perkins sees continuing havoc in supply chains. “There’s nothing settled. 2021 and 2022, I strongly believe, will be an absolute struggle for supply chain. It will be worse than 2020. It’s going to take the next nine months just for global ocean freight to re-stabilize,” he emphasized. “I think it’s another year and a half’s problem.”[nbsp]
5. Social justice movements put spotlight on diversity and inclusion
PMI believes increasing diversity within its member engagement and volunteer leadership pipeline is essential to the future of the association. PMI supports a diversity and inclusion (D[&]I) lens that identifies eligible applicants who have the range of experiences and interests – from business and marketing to manufacturing and engineering – that may best fit PMI’s needs. Many of PMI’s members have realized the fundamental value of strong D[&]I programs as well, adding new strategies, goals and tools to their endeavors.
As the pandemic persisted and race and social justice issues took center stage, PMI member UL stepped up its D[&]I efforts to support its colleagues. “What we experienced last year was this eye-opening, this awakening for corporate America,” said Katrina Jackson, UL’s global head of diversity and inclusion. While UL had already established a formal “D[&]I ecosystem” with executive and leadership councils, global ambassadors and internal business resource groups, Jackson said the company wanted to be more transparent and set out to advance equity and achieve measurable progress.
The company started with a public statement from UL President and CEO Jennifer Scanlon supporting and standing with Black colleagues and followed up with honest, transparent “inclusion conversations,” Jackson noted. Those conversations involved more than 1,000 UL leaders and colleagues sharing very private and emotional experiences. “What came of these inclusion conversations has shed such vulnerability and transparency,” Jackson said.
“This was a true turning point within UL’s D[&]I journey. And so that push and pull started to shift to more of a pull from our organization, where leaders were reaching out and saying, ‘Hey, what can we do? I want to hold space for my colleagues.’ Or even sharing, ‘I want to have these conversations, but I don’t know where to start,’” she added.
To help with those conversations, the UL D[&]I team developed a toolkit with talking points, questions and discussion topics that everyone from leaders to individual employees could use. Jackson said the toolkit was one mechanism to empower colleagues in building a “psychologically safe” environment and to enable everyone to come to work and be their whole selves. UL wanted to do more to support employees in fighting racial injustice, too. After George Floyd was killed and all the conversations about it that took place within UL’s walls, the D[&]I team worked with the corporate sustainability group to establish a matching program for racial justice to impact the Black community overall, something that employees wanted to champion.
As a result of UL’s D[&]I journey and these conversations, UL put in place its 2025 commitments to advance equity for the company’s women, people of color and LGBTQ+ populations. UL included the company’s internal business resource groups and global D[&]I ambassadors, initiated and led by employees, to foster inclusivity for various workplace communities across the globe. These groups within UL help advance their diversity objectives and are a catalyst for business growth. In addition, UL has Diversity + Inclusion Executive and Leadership Councils, which take a top-down bottom-up approach to diversity within the company.
Part of UL’s commitment to weaving D[&]I into its corporate fabric was to put together its 2020 Diversity and Inclusion Report. The report spells out the organization’s strategy, commitments, initiative and accountability goals, such as making progress on gender balance. For example, UL appointed its first female CEO in 2019 and increased female director and global leadership positions from 23% in 2019 to 25% in 2020. Jackson noted the report’s purpose, saying: “Let’s hold ourselves accountable. Let’s make meaningful progress. Let’s put priorities in place. And let’s ensure that we’re tracking and measuring along the way.”
Viega Recognizes Its Women Leaders
Viega, LLC, have recognized the benefits of promoting a diverse workforce and hiring more women. Viega recently highlighted its efforts in a series of blog articles, one of which features Kim Smith, supervisor of the molding department of Viega’s plant in McPherson, Kan., and another featuring Tricia Musgrave, Viega’s director of technical marketing. Dalyn Cantrell, senior director of national accounts and residential sales for Viega, also was featured, discussing how the industry is making inroads as more women join the ranks.[nbsp]
Make Your Voice Heard through Participation in PMI Committees
Advocacy/Government Affairs
Co-Chairs: Lowell Lampen, Kohler Co., and
Troy Benavidez, LIXIL
Allied Member Committee
Chair: Anish Desai, IAPMO
Commerce
Co-Chairs: Elton Perkins, Fluidmaster, Inc., and
Liz Renfro, Delta Faucet Co.
Technical
Co-Chairs: Ned Dickey, Hansgrohe, and
C.J. Lagan, LIXIL
Water Efficiency and Sustainability
Co-Chairs: Cambria McLeod, Kohler Co., and
Will Wang, Fluidmaster, Inc.
2020 PMI Board of Directors
President: Todd Teter, House of Rohl
Vice President: Martin Knieps, Viega, LLC
Secretary-Treasurer: Sal Gattone, LIXIL
Immediate Past President: Joel Smith, Kohler Co.
Fernando Fernandez, TOTO USA
Daniel Gleiberman, Sloan Valve Co.
Bob Neff, Delta Faucet Co.
Chip Way, Lavelle Industries, Inc.
Strategic Advisory Council
Graham Allen, Sloan Valve Co.
Shawn Oldenhoff, Kohler Co.
Ken Roberts, Delta Faucet Co.
William Strang, TOTO USA
Claude Theisen, T[&]S Brass and Bronze Works
PMI Staff
Kerry Stackpole, FASAE, CAE, CEO/Executive Director
Matt Sigler, Technical Director
Jodi Stuhrberg, Association Manager
Stephanie Lass, Education Coordinator
Ann Geier, Administrative Assistant
2021 PMI Events
PMI CEO Thinking Forum | April 21, Virtual
Emerging Water Technology Symposium | May 11-12, Virtual
PMI Virtual Legislative Forum | June 23
PMI Aspiring Leaders Program | Nov. 15, USS Midway Museum, San Diego, Calif.
PMI21 Manufacturing Success Conference | Nov. 15-18, Paradise Point, San Diego, Calif.